
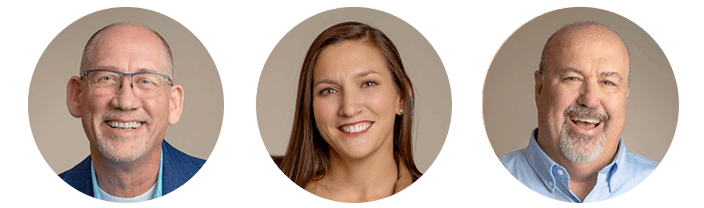
Tune in to “Crazy About Packaging”- ICPG’s podcast that delivers insightful packaging stories. Subscribe anywhere you get podcasts to elevate your packaging passion!
We’ve mastered the complexities of polypropylene packaging to create performance barrier & non-barrier structures designed to meet your exact requirements. Select from homopolymer, random copolymer, impact copolymer and custom blends paired with a vast selection of unique formulation options.
As industries search for a strong, viable solution for polystyrene (PS) replacement, many have turned to polypropylene (PP) packaging materials, as the structure is strong and versatile. PP rollstock offers a safe and sustainable solution when compared to alternative packaging materials. Explore the advantages of polypropylene packaging below.
Polypropylene is one of the lowest density and lightest weight of all rigid plastic packaging options, resulting in a 12% density reduction in comparison to polystyrene (PS) and a 30% density reduction in comparison to PET. In thermoforming and form fill seal processes, this results in higher yield, reduced cost, and less plastic used in each package.
PP’s superior performance means it is not only recyclable (even in high-barrier formulations) — it is also more sustainable at every step of the production process. Its lightweight nature leads to downstream sustainability advantages, including less CO2 equivalents, less solid waste by weight, and lower fuel consumption and emissions than other materials. Polypropylene packaging allows manufacturers to meet or exceed sustainability targets. It is easily sorted within the recycling stream using water displacement methods.
The high heat resistance offered by polypropylene means it has compatibility with hot-fill, retort, aseptic, high pressure processing, and other processing methods. Impact copolymer grades offer low temperature impact resistance making PP the ideal material for applications designed for extreme temperature changes, including freezer-to-microwave trays.
PP is available in homopolymer, random copolymer, impact copolymer, and specialty proprietary formulations, offering a vast range of specifications as well as mechanical and physical properties. This allows us to tailor polypropylene rollstock formulations to the exact requirements of an individual food packaging application, regardless of your type of packaging platform.
● Monolayer
● Laminated barrier PP
● Multi-layer coextruded barrier structures including:
– PP/EVOH/PP
– PP/EVOH/PE
● Symmetrical & asymmetrical configurations
● Thermoforming
● FFS and FS
● Aseptic
● HPP with both clear & opaque PP
● Retort
● Hot-fill
● Clear & clear-tints
● Color matching
● Custom-designed decorative lamination
● Application-based barrier specifications
● Specialty topical additive coating
● Mineral filler blending
● One & two-side corona treatment
● Performance additive integration
● Snap-able PP for FFS and FS applications
● UltraClear Homopolymer PP for high temperature applications
● Clarified Impact Copolymer PP for low & high temperature applications
● Clarified Impact Copolymer PP for HPP applications
Historically, polystyrene was the material of choice for packaging due to its performance and versatility for FFS applications. However, it is becoming increasingly clear that PS is not sustainable or entirely safe for many of today’s applications.
For this reason, PP has been recognized as one of the primary PS material replacement options for FFS applications. However, switching to PP has come with its own challenges; many attempts have been made to develop a polypropylene-based solution for form-fill-seal applications, only to result in significant downstream processing challenges and compromise to part performance.
ICPG is changing that. Our new XPP Polypropylene Solutions bring the savings and sustainability of traditional PP materials — while matching the performance of PS and offering a lower total-cost-of-ownership solution that is compatible with existing FFS equipment. This is the first packaging material of its kind, and ICPG is excited to bring this solution to the industry.
Looking for the perfect packaging solution for your applications? A material solutions expert at ICPG can help you determine the best fit polymer for your needs.
Learn about our longstanding commitment to fully certified food packaging solutions.
Find Out MoreExplore our selection of specialty polypropylene packaging solutions.
Find Out MoreUncover an expertly crafted collection of food packaging know-how in our Industry Insights blog.
Find Out MoreDiscover how our methods and materials reduce, reuse, recycle and reinforce our everyday dedication to sustainability.
Find Out MoreTrying something brand new? Tap into our on-site technical support services to help you through the development process— one material at a time.
Find Out More