
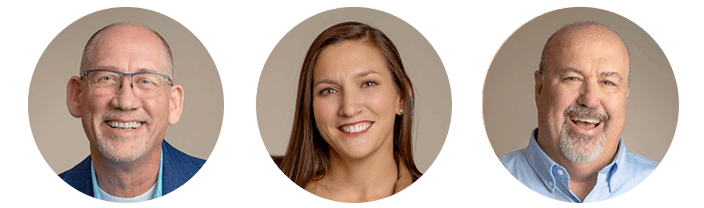
Tune in to “Crazy About Packaging”- ICPG’s podcast that delivers insightful packaging stories. Subscribe anywhere you get podcasts to elevate your packaging passion!
ICPG helps processors create the perfect form fill seal packaging for their applications.
Form fill seal production lines for rigid packaging applications are designed to combine multiple processes into one system. Integrating thermoforming, filling, sealing, and die-cutting into one process enables the form fill seal lines to efficiently form containers that are then precisely filled with the target food product, such as yogurt and pudding, then sealed ready for distribution.
The process starts with a large reel of rigid rollstock which is heated by contact plates to become formable. This sheet then moves to the forming station where cups are formed through the traditional thermoforming process. Remaining in the “web”, these cups move to the filling and sealing stations, where the cups are filled with product and sealed with lidding film. Next, the filled and sealed cups advance to the die cutting station, where they are cut from the “web” into finished products, such as multipacks, and proceed to automated secondary packaging lines for final, retail-ready packaging with minimal labor.
● Monolayer
● Multi-layer barrier & non-barrier coextrusion
● Symmetrical & asymmetrical structures
● XPP Polypropylene Solutions
● Barrier materials:
– EVOH
– Reimagined barrier technology (RE-BA)
● Polystyrene (PS)
● PET
● Barrier Materials:
– EVOH
● Custom colors
● Clear & clear-tinted PP & PS
● Performance additives
● Topical additive anti-fog and silicone coating
● Custom barrier specifications
● Custom development process
● Design consultation
● On-site technical support
Historically, polystyrene (PS) has been the material of choice for form fill seal (FFS) applications. However, the industry has evolved in response to concerns over material recyclability and food safety. For this reason, it’s essential to choose the right material: one that is food-safe, sustainable, and can meet the requirements for your specific application. If you’re still searching for the right FFS material, ICPG can help. We offer a range of high-quality material options, and our experts will work with you to select the right material for your form fill seal applications.
Looking for the perfect packaging solution for your applications? A material solutions expert at ICPG can help you determine the best polymer for your needs.
Trying something brand new? Tap into our on-site technical support services to help you through the development process— one material at a time.
Uncover an expertly crafted collection of food packaging know-how in our Industry Insights blog.
Find Out MoreDiscover how our methods and materials reduce, reuse, recycle and reinforce our everyday dedication to sustainability.
Find Out MoreLet’s collaborate to advance innovation. Explore exactly what your customized packaging is capable of.